Вода из реки профильтровывается через песок и накапливается в скважине. Приток воды из скважины форсируется вакуум-насосом или водоподъемным насосом и подается на кустовую насосную станцию (КНС). При открытом методе воду с помощью насосов первого подъема откачивают из реки и подают на водоочистную станцию, где она проходит цикл очистки и попадает в отстойник. В отстойнике с помощью реагентов-коагуляторов частицы механических примесей и соединений железа выводятся в осадок. Окончательная очистка воды происходит в фильтрах, где в качестве фильтрирующих материалов используют чистый песок или мелкий уголь.
Все оборудование системы сбора и подготовки нефти и воды поставляют в комплектно-блочном исполнении в виде полностью готовых блоков и суперблоков.
Магистральные нефтепроводы. Часть 1
Помните пословицу: «За морем телушка — полушка, да рубль перевоз...» Она как нельзя лучше характеризует важность транспортной проблемы. Можно, используя последние достижения науки и техники, добыть очень дешевое сырье. Но не забывайте:
большинство нефтепромыслов в настоящее время находится далеко от нефтеперерабатывающих предприятий.
Можно, конечно, использовать традиционные виды транспорта. На море грузить добываемую нефть в танкеры, на суше в железнодорожные цистерны. Но выгодно ли это?
Даже на море, где современные супертанкеры забирают в трюмы сразу сотни тысяч тонн топлива, такое решение транспортной проблемы нельзя назвать наилучшим. Ведь подобная транспортировка не так уж дешева. Вдобавок, частые аварии танкеров приводят к загрязнению окружающей среды, уничтожают все живое на сотни миль вокруг, да и регулярность такого сообщения могла бы быть лучшей: как известно, и по сию пору скорость движения морского транспорта во многом зависит от погоды.
Еще хуже дела обстоят на суше. Для перевозки топлива нам понадобилось бы с каждым годом строить все новые и новые железные дороги, по которым сновали бы бесчисленные составы цистерн. А уж с газом еще хуже: вместо цистерн пришлось бы заводить целый парк специальных «термосов», в которых бы постоянно поддерживалась температура минус 80 градусов Цельсия и ниже при давлении 5—б МПа — только так можно перевозить газ в жидком состоянии.
Собственно так и поступают, например, при транспортировке метана из Алжира в США. Создан целый флот танкеров-метановозов. У них на борту работают специальные компрессорные и холодильные установки, поддерживающие нужный режим в танкерах, с тем, чтобы метан был в нужном (жидком) агрегатном состоянии. Во время рейса часть перевозимого метана расходуется на работу холодильных установок.
Число таких плавучих «термосов» исчисляется десятками. В то же время трудно представить себе такую транспортную технологию в сухопутном исполнении.
По счастью, мы можем обо всем этом говорить в сослагательном наклонении. Специалисты нашли другое решение транспортной проблемы. По всей стране и за ее рубежи проложена мощная и разветвленная сеть трубопроводов, и развитие этой сети продолжается.
Трубопроводы в нашей стране по темпам роста грузооборота намного опередили другие виды транспорта. Доля их в общем объеме перевозок быстро росла и достигла почти трети общего грузооборота страны. Столь стремительные темпы объясняются исключительно высокой экономичностью трубопроводов. Достаточно сказать, что на доставку каждой тонны нефти по трубам требуется в 10 с лишним раз меньше трудовых затрат, чем для ее перевозки по железным дорогам. Этот прогрессивный вид транспорта экономит ежегодно труд примерно 750 тысяч человек!
В настоящее время трубопроводный транспорт становится средоточием новейших достижений отечественной науки и техники. Казалось бы, что тут хитрого: труба она и есть труба... Но само по себе изготовить трубу, да еще большого диаметра — достаточно сложная инженерно-техническая задача. Тем не менее, в короткий срок производство таких труб было налажено на предприятиях нашей страны.
Другая проблема при строительстве нефтегазопровода — все трубы необходимо герметично сваривать в единую нитку, и притом довольно длинную: тот же газопровод Уренгой — Помарьи — Ужгород имеет протяженность около 4500 километров!
А общая протяженность сварных швов, как показывают расчеты, в 1,5 раза превышает длину самого трубопровода.
Систематическое сооружение нефтепроводов в районах добычи нефти — в Урало-Поволжье и Закавказье было начато в середине 60-х годов, прошлого века В этот период, в частности, были построены трансконтинентальные нефтепроводы Туймазы—Омск (впервые применены трубы диаметром 530 мм), Туймазы — Омск — Новосибирск — Иркугск диаметром 720 мм и длиной 3662 км, нефтепроводы Альметьевск — Горький (первая нитка) Альметьевск — Пермь, Ишимбай — Орск, Горький — Рязань, Тихорецк — Туапсе, Рязань — Москва и др. Необходимо особо отметить, что в 1955 г. был введен в эксплуатацию первый «горячий» нефтепровод Озек-Суат — Грозный диаметром 325 мм и протяженностью 144 км; по нему впервые в нашей стране стали транспортировать нефть после предварительного подогрева в специальных печах.
В 1964 г. был введен в эксплуатацию крупнейший в мире по протяженности (5500 км вместе с ответвлениями) трансевропейский нефтепровод «Дружба», соединяющий месторождения нефти в Татарии и Куйбышевской области с восточно-европейскими странами (Чехия, Словакия, Венгрия, Польша, Германия).
Открытие крупнейших месторождений нефти в Западной Сибири в корне изменило приоритеты трубопроводного строительства. Транспортировка нефти из данного региона до существовавших промышленных центров была крайне затруднена. Расстояние от месторождений до ближайшей железнодорожной станции составляло более 700 км. Единственная транспортная магистраль — река Обь и впадающая в нее река Иртыш — судоходны не более 6 мес. в году. Обеспечить транспортировку все возрастающих объемов нефти мог только трубопроводный транспорт.
В декабре 1965 г. было завершено строительство и введен в эксплуатацию первый в Сибири нефтепровод Шаим — Тюмень диаметром 529— 720 мм и протяженностью 410 км. В ноябре 1965 г. начато и в октябре 1967 г. завершено строительство нефтепровода Усть-Балык — Омск диаметром 1020 мм и протяженностью 964 км (в США трубопроводов такого диаметра еще не было) Осенью 1967 г. начато и в апреле 1969 г. завершено строительство нефтепровода Нижневартовск — Усть-Балык диаметром 720 мм и протяженностью 252 км. В последующие годы на базе Западно-Сибирских месторождений были построены трансконтинентальные нефтепроводы Усть-Балык — Курган — Уфа — Альметьевск (1973 г.), Александровское — Анжеро-Судженск — Красноярск — Иркутск (1973 г.), Нижневартовск — Курган — Куйбышев (1976 г.), Сургут — Горький — Полоцк (1979 г.) и др.
Продолжалось строительство нефтепроводов и в других регионах. В 1961 г. на месторождениях Узень и Жетыбай (Южный Мангышлак) были получены первые фонтаны нефти, а уже в апреле 1966 г. вступил в строй нефтепровод Узень — Шевченко длиной 141,6 км. В дальнейшем он был продлен сначала до Гурьева (1969 г.), а затем до Куйбышева (1971 г.). Ввод в эксплуатацию нефтепровода Узень — Гурьев — Куйбышев диаметром 1020 мм и протяженностью 1750 км позволил решить проблему транспорта высоковязкой и высокозастывающей нефти Мангышлака. Для этого была выбрана технология перекачки с предварительным подогревом в специальных печах. Нефтепровод Узень — Гурьев — Куйбышев стал крупнейшим «горячим» трубопроводом мира.
Были продлены нефтепроводы Альметьевск — Горький и Туймазы — Омск — Новосибирск на участках соответственно Горький — Ярославль — Кириши и Новосибирск — Красноярск — Иркутск.
На других направлениях в 1971 — 1975 гг. были построены нефтепроводы Уса — Ухта — Ярославль — Москва, Куйбышев — Тихорецкая — Новороссийск и другие. В 1976— 1980 гг. — нефтепроводы Куйбышев — Лисичанск — Одесса, Холмогоры — Сургут, Омск — Павлодар, Каламкас — Шевченко, Самгори — Батуми и другие, в 1981— 1985 гг. — нефтепроводы Холмогоры — Пермь — Альметьевск — Клин, Возей — Уса — Ухта, Кенкияк — Орск, Павлодар — Чимкент — Чардар — Фергана, Прорва — Гурьев, Красноленинский — Шаим, Тюмень — Юргамыш, Грозный — Баку.
В настоящее время все магистральные нефтепроводы России эксплуатируются ОАО «АК Транснефть», которое является транспортной компанией и объединяет 11 российских предприятий трубопроводного транспорта нефти, владеющих нефтяными магистралями, эксплуатирующих и обслуживающих их. При движении от грузоотправителя до грузополучателя нефть проходит в среднем 3 тыс. км. ОАО «АК Транснефть» разрабатывает наиболее экономичные маршруты движения нефти, тарифы на перекачку и перевалку нефти с утверждением их в Федеральной энергетической комиссии (ФЭК).
Взаимоотношения ОАО АК «Транснефть» с грузоотправителями регулируются «Положением о приеме и движении нефти в системе магистральных нефтепроводов», утвержденным Минэнерго РФ в конце 1994 г. Этот документ включает методику определения оптимальных объемов поставки нефти и газового конденсата на нефтеперерабатывающих заводах (НПЗ) России, квот нефтеперерабатывающих предприятий для поставки на экспорт, порядок составления ежеквартальных графиков транспортировки нефти для каждого из производителей (с разбивкой по месяцам). Документ провозглашает равнодоступность всех грузоотправителей к системе трубопроводного транспорта.
По состоянию на 2002 г. ОАО АК «Транснефть» эксплуатировала 48,6 тыс. км магистральных нефтепроводов диаметром от 400 до 1220 мм, 322 нефтеперекачивающие станции, резервуары общим объемом по строительному номиналу 13,5 млн м3. 32% нефтепроводов имели срок эксплуатации до 20 лет, 34% — от 20 до 30 лет и свыше 30 лет эксплуатируется 34% нефтепроводов. Компания выполняет собственными силами и средствами практически весь комплекс профилактических и ремонтно-восстановительных работ на всех объектах магистральных нефтепроводов. В состав нефтепроводных предприятий входят 190 аварийно-восстановительных пунктов, 71 ремонтно-строительная колонна для выполнения капитального ремонта линейной части, 9 центральных (региональных) без производственного обслуживания и ремонта и 38 баз производственного обслуживания. В мае 1991 г. в компании создан Центр технической диагностики, ОАО ЦТД «Диаскан», который обеспечивает проведение диагностики магистральных нефтепроводов.
К настоящему времени нефть различных месторождений поступает на отечественные нефтеперерабатывающие заводы и экспорт по системе нефтепроводов ОАО «Транснефть».
Магистральные нефтепроводы. Часть 2
Нефтепроводом принято называть трубопровод, предназначенный для перекачки нефти и нефтепродуктов (при перекачке нефтепродукта иногда употребляют термин нефтепродуктопровод). В зависимости от вида перекачиваемого нефтепродукта трубопровод называют также бензино-, керосин-, мазутопроводом и т.д.
По своему назначению нефте- и нефтепродуктопроводы можно разделить на следующие группы:
промысловые— соединяющие скважины с различными объектами и установками подготовки нефти на промыслах;
магистральные (МН)— предназначенные для транспортировки товарной нефти и нефтепродуктов (в том числе стабильного конденсата и бензина) из районов их добычи (от промыслов) производства или хранения до мест потребления (нефтебаз, перевалочных баз, пунктов налива в цистерны, нефтеналивных терминалов, отдельных промышленных предприятий и НПЗ). Они характеризуются высокой пропускной способностью, диаметром трубопровода от 219 до 1400 мм и избыточным давлением от 1,2 до 10 МПа;
технологические— предназначенные для транспортировки в пределах промышленного предприятия или группы этих предприятий различных веществ (сырья, полуфабрикатов, реагентов, а также промежуточных или конечных продуктов, полученных или используемых в технологическом процессе и др.), необходимых для ведения технологического процесса или эксплуатации оборудования.
Согласно СНиП 2.05.06 — 85 магистральные нефте- и нефтепродуктопроводы подразделяются на четыре класса в зависимости от условного диаметра труб (в мм): 1 — 1000—1200 включительно: II — 500—1000 включительно; III — 300—500 включительно; IУ — 300 и менее
Наряду с этой классификацией СНиП 2.05.07 — 85 устанавливает для магистральных нефтепроводов категории, которые требуют обеспечения соответствующих прочностных характеристик на любом участке трубопровода:
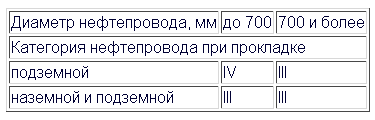
Приведенная классификация и категории трубопроводов определяют в основном требования, связанные с обеспечением прочности или неразрушимости труб. В северной природно-климатической зоне все трубопроводы относятся к категории III. Исходя из этих же требований в СНиП 2.05.06 — 85 определены также и категории, к которым следует относить не только трубопровод в целом, но и отдельные его участки. Необходимость в такой классификации объясняется различием условий, в которых будет находиться трубопровод на тех или иных участках местности, и возможными последствиями в случае разрушения трубопровода на них. Отдельные участки нефтепроводов могут относиться к высшей категории В, категории I или II. К высшей категории В относятся трубопроводные переходы через судо- и несудоходные реки при диаметре трубопровода 1000 мм и более. К участкам категории I относятся под- и надводные переходы через реки, болота типов II и III, горные участки, вечномерзлые грунты.
К участкам категории II относятся под- и надводные переходы через реки, болота типа и, косогорные участки, переходы под дорогами и т.д.
Прокладку трубопроводов можно осуществлять одиночно и параллельно действующим или проектируемым магистральным трубопроводам в техническом коридоре. Под техническим коридором магистральных трубопроводов согласно СНиП 27.05.06—85 понимают систему параллельно проложенных трубопроводов по одной трассе. В отдельных случаях допускается прокладка нефте- и газопроводов в одном коридоре.
Технологические трубопроводы в зависимости от физико-химических свойств и рабочих параметров (давления Р и температуры Т) подразделяются на три группы (А, Б, В) и пять категорий. Группу и категорию технологического трубопровода устанавливают по параметру, который требует отнесения его к более ответственной группе или категории. Класс опасности вредных веществ следует определять по ГОСТ 12.1.005—76 и ГОСТ 12.01.007—76, взрывопожароопасность — по ГОСТ 12.1.004—76. Нефти имеют класс опасности II, масла минеральные нефтяные — III, бензины — IV.
Для технологических трубопроводов нефтеперекачиваюших станций важное значение имеет правильный выбор параметров транспортируемого вещества. Рабочее давление принимается равным избыточному максимальному давлению, развиваемому насосом, компрессором или другим источником давления, или давлению, на которое отрегулированы предохранительные устройства. Рабочую температуру принимают равной максимальной или минимальной температуре транспортируемого вещества, установленной технологическим регламентом или другим нормативным документом (СНиП, РД, СН п т.д.).
Состав сооружений магистральных нефтепроводов
рис 20.1.
В состав магистральных нефтепроводов входят: линейные сооружения, головные и промежуточные перекачивающие и наливные насосные станции и резервуарные парки (рис. 20.1). В свою очередь линейные сооружения согласно СНиП 2.05.06 — 85 включают: трубопровод (от места выхода с промысла подготовленной к дальнему транспорту товарной нефти) с ответвлениями и лупингами, запорной арматурой, переходами через естественные и искусственные препятствия, узлами подключения нефтеперекачивающих станций, узлами пуска и приема очистных устройств и разделителей при последовательной перекачке, установки электрохимической защиты трубопроводов от коррозии, линии и сооружения технологической связи, средства телемеханики трубопровода, линии электропередачи, предназначенные для обслуживания трубопроводов, и устройства электроснабжения и дистанционного управления запорной арматурой и установками электрохимической защиты трубопроводов; противопожарные средства, противоэррозионные и защитные сооружения трубопровода; емкости для хранения и разгазирования конденсата, земляные амбары для аварийного выпуска нефти, здания и сооружения линейной службы эксплуатации трубопроводов; постоянные дороги и вертолетные площадки, расположенные вдоль трассы трубопровода, и подъезды к ним, опознавательные и сигнальные знаки местонахождения трубопровода; пункты подогрева нефти указатели и предупредительные знаки.
Основные элементы магистрального трубопровода — сваренные в непрерывную нитку трубы, представляющие собой собственно трубопровод. Как правило, магистральные трубопроводы заглубляют в грунт обычно на глубину 0,8 м до верхней образующей трубы, если большая или меньшая глубина заложения не диктуется особыми геологическими условиями или необходимостью поддержания температуры перекачиваемого продукта на определенном уровне (например для исключения возможности замерзания скопившейся воды) Для магистральных трубопроводов применяют цельнотянутые илы сварные трубы диаметром 300—1420 мм. Толщина стенок труб определяется проектным давлением в трубопроводе, которое может достигать 10 МПа. Трубопровод, прокладываемый по районам с вечномерзлыми грунтами или через болота, можно укладывать на опоры или в искусственные насыпи.
На пересечениях крупных рек нефтепроводы иногда утяжеляют закрепленными на трубах грузами или сплошными бетонными покрытиями закрепляют специальными анкерами и заглубляют ниже дна реки. Кроме основной, укладывают резервную нитку перехода того же диаметра. На пересечениях железных и крупных шоссейных дорог трубопровод проходит в патроне из труб, диаметр которых на 100—200 мм больше диаметра трубопровода.
С интервалом 10—30 км в зависимости от рельефа трассы на трубопроводе устанавливают линейные задвижки для перекрытия участков в случае аварии или ремонта.
Вдоль трассы проходит линия связи (телефонная, радиорелейная), которая в основном имеет диспетчерское назначение. Ее можно использовать для передачи сигналов телеизмерения и телеуправления. Располагаемые вдоль трассы станции катодной и дренажной защиты, а также протекторы защищают трубопровод от наружной коррозии, являясь дополнением к противокоррозионному изоляционному покрытию трубопровода.
Нефтеперекачивающие станции (НПС) располагаются на нефтепроводах с интервалом 70—150 км. Перекачивающие (насосные) станции нефтепроводов и нефтепродуктопроводов оборудуются, как правило, центробежными насосами с электроприводом. Подача применяемых в настоящее время магистральных насосов достигает 12500 м3/ч. В начале нефтепровода находится головная нефтеперекачивающая станция (ГНПС), которая располагается вблизи нефтяного промысла или в конце подводящих трубопроводов, если магистральный нефтепровод обслуживают несколько промыслов или один промысел разбросанный на большой территории, ГНПС отличается от промежуточных наличием резервуарного парка объемом, равным двух-, трехсуточной пропускной способности нефтепровода. Кроме основных объектов, на каждой насосной станции имеется комплекс вспомогательных сооружений: трансформаторная подстанция, снижающая подаваемое по линии электропередач (ЛЭП) напряжения от 110 или 35 до 6 кВ, котельная, а также системы водоснабжения, канализации, охлаждения и т.д. Если длина нефтепровода превышает 800 км, его разбивают на эксплуатационные участки длиной 100—300 км, в пределах которых возможна независимая работа насосного оборудования. Промежуточные насосные станции на границах участков должны располагать резервуарным парком объемом, равным 0,3—1,5 суточной пропускной способности трубопровода. Как головная, так и промежуточные насосные станции с резервуарными парками оборудуются подпорными насосами. Аналогично устройство насосных станций магистральных нефтепродуктопроводов.
Тепловые станции устанавливают на трубопроводах, транспортирующих высоко застывающие и высоковязкие нефти и нефтепродукты иногда их совмещают с насосными станциями. Для подогрева перекачиваемого продукта применяют паровые или огневые подогреватели (печи подогрева) для снижения тепловых потерь такие трубопроводы могут быть снабжены теплоизоляционным покрытием.
По трассе нефтепровода могут сооружаться наливные пункты для перевалки и налива нефти в железнодорожные цистерны.
Конечный пункт нефтепровода — либо сырьевой парк нефтеперерабатывающего завода, либо перевалочная нефтебаза, обычно морская, откуда нефть танкерами перевозится к нефтеперерабатывающим заводам или экспортируется за границу.
Краткое описание основных технологических процессов топливного производства
Сущность нефтеперерабатывающего производства
Процесс переработки нефти можно разделить на 3 основных этапа:
1. Разделение нефтяного сырья на фракции, различающиеся по интервалам температур кипения
(первичная переработка);
2. Переработка полученных фракций путем химических превращений содержащихся в них углеводородов и выработка компонентов товарных нефтепродуктов
(вторичная переработка);
3. Смешение компонентов с вовлечением, при необходимости, различных присадок, с получением товарных нефтепродуктов с заданными показателями качества
(товарное производство).
Продукцией НПЗ являются моторные и котельные топлива, сжиженные газы, различные виды сырья для нефтехимических производств, а также, в зависимости от технологической схемы предприятия - смазочные, гидравлические и иные масла, битумы, нефтяные коксы, парафины. Исходя из набора технологических процессов, на НПЗ может быть получено от 5 до более, чем 40 позиций товарных нефтепродуктов.
Нефтепереработка - непрерывное производство, период работы производств между капитальными ремонтами на современных заводах составляет до 3-х лет. Функциональной единицей НПЗ является технологическая
установка- производственный объект с набором оборудования, позволяющего осуществить полный цикл того или иного технологического процесса.
В данном материале кратко описаны основные технологические процессы топливного производства - получения моторных и котельных топлив, а также кокса.
Поставка и приём нефти
В России основные объёмы сырой нефти, поставляемой на переработку, поступают на НПЗ от добывающих объединений по магистральным нефтепроводам. Небольшие количества нефти, а также газовый конденсат, поставляются по железной дороге. В государствах-импортёрах нефти, имеющих выход к морю, поставка на припортовые НПЗ осуществляется водным транспортом.
Принятое на завод сырьё поступает в соответствующие емкости
товарно-сырьевой базы(рис.1), связанной трубопроводами со всеми технологическими установками НПЗ. Количество поступившей нефти определяется по данным приборного учёта, или путём замеров в сырьевых емкостях.
Подготовка нефти к переработке (электрообессоливание)
Сырая нефть содержит соли, вызывающие сильную коррозию технологического оборудования. Для их удаления нефть, поступающая из сырьевых емкостей, смешивается с водой, в которой соли растворяются, и поступает на ЭЛОУ -
электрообессоливащую установку(рис.2). Процесс обессоливания осуществляется в
электродегидраторах- цилиндрических аппаратах со смонтированными внутри электродами. Под воздействием тока высокого напряжения (25 кВ и более), смесь воды и нефти (эмульсия) разрушается, вода собирается внизу аппарата и откачивается. Для более эффективного разрушения эмульсии, в сырьё вводятся специальные вещества -
деэмульгаторы. Температура процесса - 100-120°С.
Первичная переработка нефти
Обессоленная нефть с ЭЛОУ поступает на установку атмосферно-вакуумной перегонки нефти, которая на российских НПЗ обозначается аббревиатурой АВТ -
атмосферно-вакуумная трубчатка. Такое название обусловлено тем, что нагрев сырья перед разделением его на фракции, осуществляется в змеевиках
трубчатых печей(рис.6) за счет тепла сжигания топлива и тепла дымовых газов.
АВТ разделена на два блока -
атмосферной и вакуумной перегонки.
1. Атмосферная перегонка
Атмосферная перегонка (рис. 3,4) предназначена для отбора
светлых нефтяных фракций- бензиновой, керосиновой и дизельных, выкипающих до 360°С, потенциальный выход которых составляет 45-60% на нефть. Остаток атмосферной перегонки - мазут.
Процесс заключается в разделении нагретой в печи нефти на отдельные фракции в
ректификационной колонне- цилиндрическом вертикальном аппарате, внутри которого расположены
контактные устройства (тарелки), через которые пары движутся вверх, а жидкость - вниз. Ректификационные колонны различных размеров и конфигураций применяются практически на всех установках нефтеперерабатывающего производства, количество тарелок в них варьируется от 20 до 60. Предусматривается подвод тепла в нижнюю часть колонны и отвод тепла с верхней части колонны, в связи с чем температура в аппарате постепенно снижается от низа к верху. В результате сверху колонны отводится бензиновая фракция в виде паров, а пары керосиновой и дизельных фракций конденсируются в соответствующих частях колонны и выводятся, мазут остаётся жидким и откачивается с низа колонны.
2. Вакуумная перегонка
Вакуумная перегонка (рис.3,5,6) предназначена для отбора от мазута
масляных дистиллятовна НПЗ топливно-масляного профиля, или широкой масляной фракции
(вакуумного газойля)на НПЗ топливного профиля. Остатком вакуумной перегонки является гудрон.
Необходимость отбора масляных фракций под вакуумом обусловлена тем, что при температуре свыше 380°С начинается термическое разложение углеводородов
(крекинг), а конец кипения вакуумного газойля - 520°С и более. Поэтому перегонку ведут при остаточном давлении 40-60 мм рт. ст., что позволяет снизить максимальную температуру в аппарате до 360-380°С.
Разряжение в колонне создается при помощи соответствующего оборудования, ключевыми аппаратами являются паровые или жидкостные
эжекторы(рис.7).
3. Стабилизация и вторичная перегонка бензина
Получаемая на атмосферном блоке бензиновая фракция содержит газы (в основном пропан и бутан) в объёме, превышающем требования по качеству, и не может использоваться ни в качестве компонента автобензина, ни в качестве товарного прямогонного бензина. Кроме того, процессы нефтепереработки, направленные на повышение октанового числа бензина и производства ароматических углеводородов в качестве сырья используют узкие бензиновые фракции. Этим обусловлено включение в технологическую схему переработки нефти данного процесса (рис.4), при котором от бензиновой фракции отгоняются сжиженные газы, и осуществляется её разгонка на 2-5 узких фракций на соответствующем количестве колонн.
Продукты первичной переработки нефти охлаждаются в
теплообменниках, в которых отдают тепло поступающему на переработку холодному сырью, за счет чего осуществляется экономия технологического топлива, в
водяных и воздушных холодильникахи выводятся с производства. Аналогичная схема теплообмена используется и на других установках НПЗ.
Современные установки первичной переработки зачастую являются комбинированными и могут включать в себя вышеперечисленные процессы в различной конфигурации. Мощность таких установок составляет от 3 до 6 млн. тонн по сырой нефти в год.
На заводах сооружается несколько установок первичной переработки во избежание полной остановки завода при выводе одной из установок в ремонт.
Продукты первичной переработки нефти
Фотографии установок первичной переработки различной конфигурации
Рис.3. Установка ЭЛОУ-АВТ-6 Саратовского НПЗ. В центре - атмосферная колонна (показаны точки отбора фракций), справа - вакуумная.
Рис.4. Установки вторичной перегонки бензина и атмосферной перегонки на НПЗ "Славнефть-ЯНОС" (слева направо).
Рис.5. Установка вакуумной перегонки мощностью 1,5 млн. тонн в год на Туркменбашинском НПЗ по проекту фирмы Uhde.
Рис. 6. Установка вакуумной перегонки мощностью 1,6 млн. тонн в год на НПЗ "ЛУКОЙЛ-ПНОС". На переднем плане - трубчатая печь (жёлтого цвета).
Рис.7. Вакуумсоздающая аппаратура фирмы Graham. Видны 3 эжектора, в которые поступают пары с верха колонны.
Вторичная переработка (начало)
Продукты первичной переработки нефти, как правило, не являются товарными нефтепродуктами. Например, октановое число бензиновой фракции составляет около 65 пунктов, содержание серы в дизельной фракции может достигать 1,0% и более, тогда как норматив составляет, в зависимости от марки, от 0,005% до 0,2%. Кроме того, тёмные нефтяные фракции могут быть подвергнуты дальнейшей квалифицированной переработке.
В связи с этим, нефтяные фракции поступают на установки вторичных процессов, призванные осуществить улучшение качества нефтепродуктов и углубление переработки нефти.
Приведённые в статье параметры технологических режимов, размеров аппаратов, выходов продуктов в целом приводятся справочно, так как в каждом конкретном случае могут варьироваться в зависимости от качества сырья, заданных параметров продуктов, выбранного аппаратурного оформления, типов применяемых катализаторов и других факторов.
Углеводороды, входящие в состав нефти и нефтепродуктов
Поскольку при описании процессов вторичной переработки используются наименования групп углеводородов, входящих в состав нефти и нефтепродуктов, приведём краткие описания данных групп и влияние углеводородного состава на показатели качества нефтепродуктов.